Centrifugal pump minimum flow recirculation
reducing cavitation
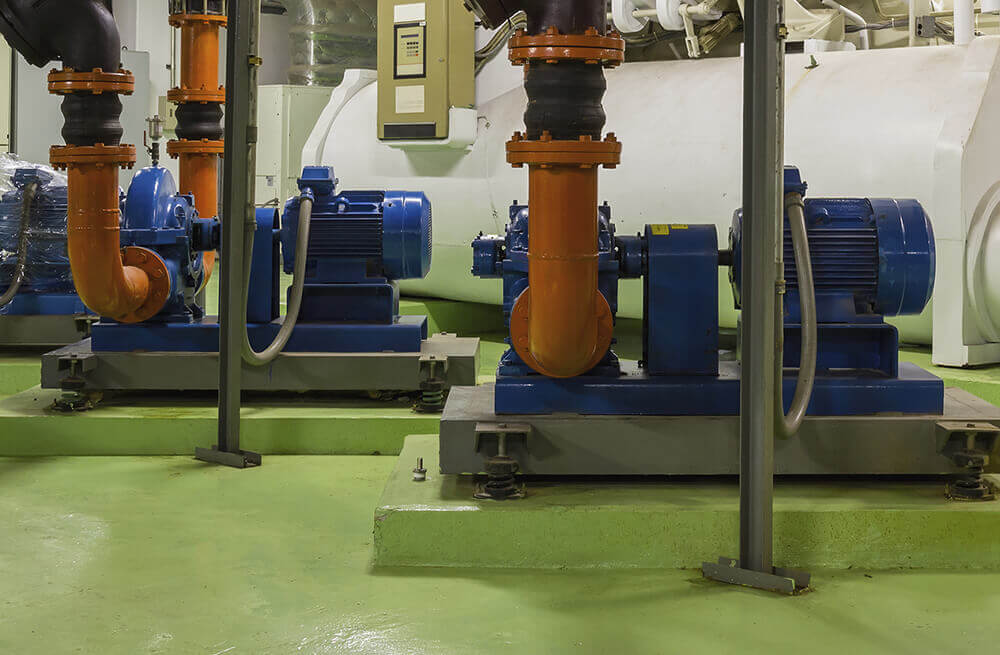
Cavitation occurs on liquid applications when drops in pressure cause vapour bubbles (cavities) to form within the liquid. As these bubbles collapse, shock waves are created which can impact on the metallic surface of the valve or trim. Though the shock waves may be small, cavitation can result in brand new equipment being out of service within minutes, in extreme cases.
Correct specification is vital to avoiding severe damage from cavitation. To bring cavitation under control it is usually necessary to stage pressure drops gradually, using specially-designed multi-stage trims. Often, where problems still arise it is because the pressure drop has not been staged sufficiently and is too sudden causing vapour bubbles to form.
Case study
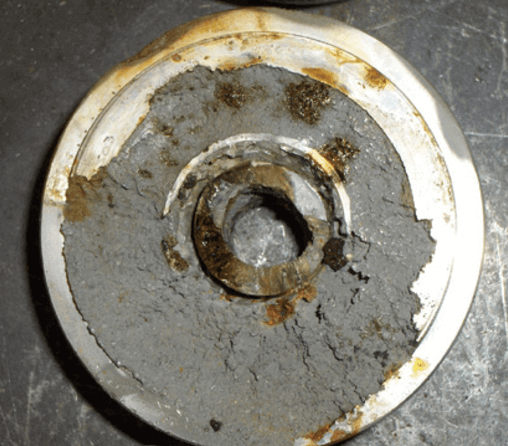
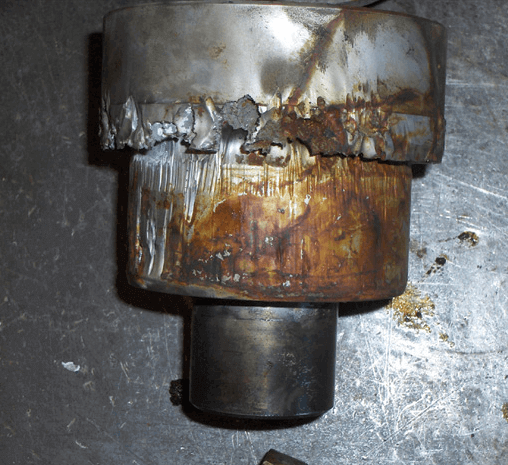
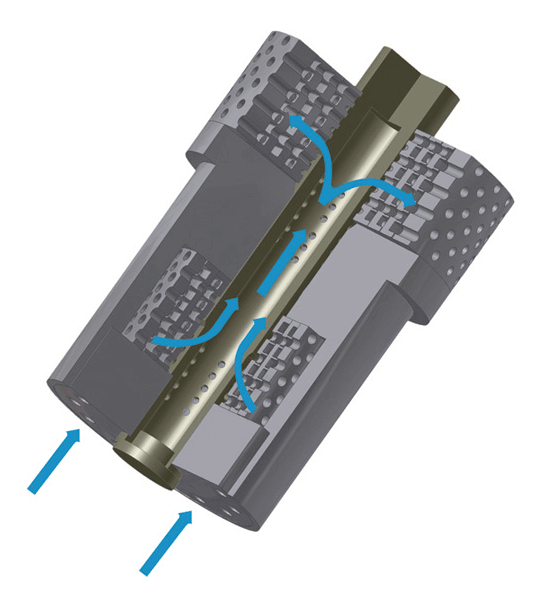
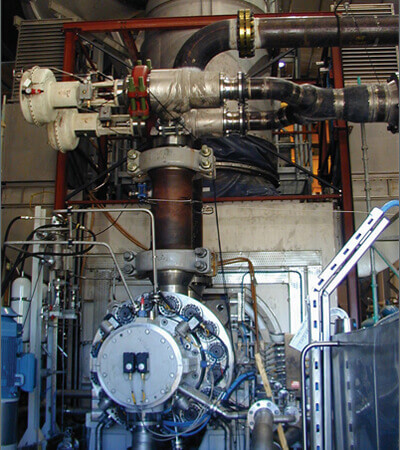
Our many accreditations and processes give you peace of mind when buying from Kent Introl. These include OHSAS 18001, ISO9001, ISO/TS29001, ISO14001, PED Certificate API 6A, API 17D Monogram and more. Visit our Accreditations page to find out more.
We continually invest in all areas of the design, testing and manufacturing process to bring you the right products at the right time, at a competitive price. This gives us ever-greater control over the timing and quality of all aspects of the manufacturing process. Visit our Research and Development page to find out more.
We can assist you right through the lifecycle of your valves and other equipment. Whether you need hands-on servicing and support, or technical training to help your own team, we have the expertise to help you maximise the performance of your valves. Visit our Services page to find out more.