Separator Level Control
tailored solutions
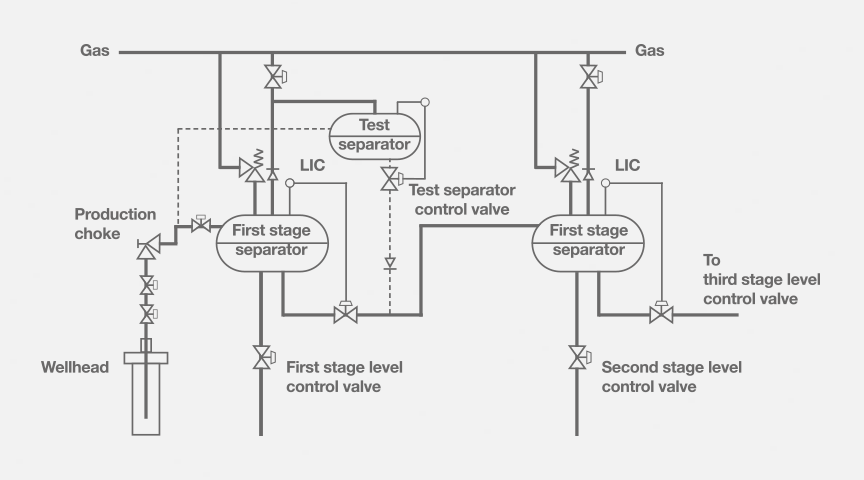
Case Study
As far back as 1974, we supplied a number of control valves for a separator level control system. The diagram above shows a schematic of the system. The original trim was an HFD cage-guided design with an operating pressure drop of 100 bar (1450psi).
Several years later in the early 1980s, the client introduced water injection, resulting in the fluid being contaminated with sand. Within two weeks of operation the valve trim was severely eroded due to the excess sand contamination. This image shows the extent of the damage caused.
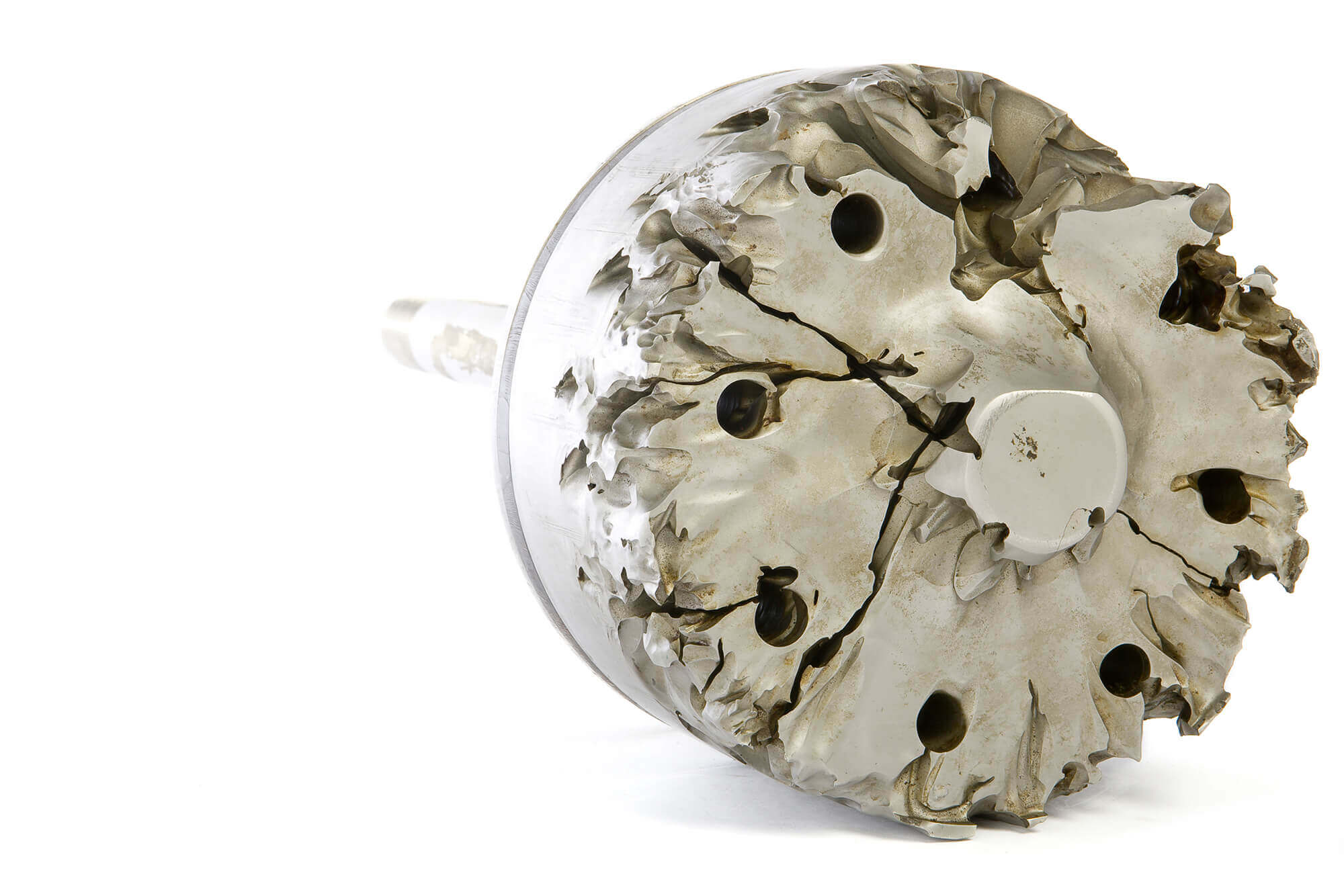
Over the next two years we developed the LCV trim design. This included various improvements to allow the valve to withstand the erosive nature of the medium. These included the introduction of a dead-band, sacrificial plug nose, shrouded seat face arrangement and solid tungsten carbide for the main trim control elements.
This diagram shows the new design features. The key features of this design were patented and still form the basis of our current severe service choke trim design as well as being an option within the globe control valve product range. The trim design used tungsten carbide resulting in a significantly lower level of erosion to the sacrificial elements even after two years of operation.
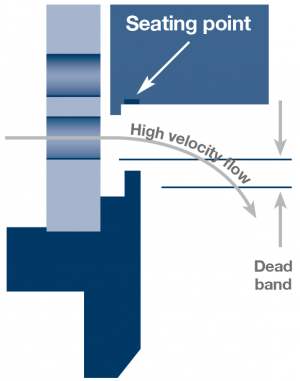
This image shows some inevitable signs of wear and tear. However even after two years the severe damage which put their previous valve out of service in just two weeks, had been completely avoided.
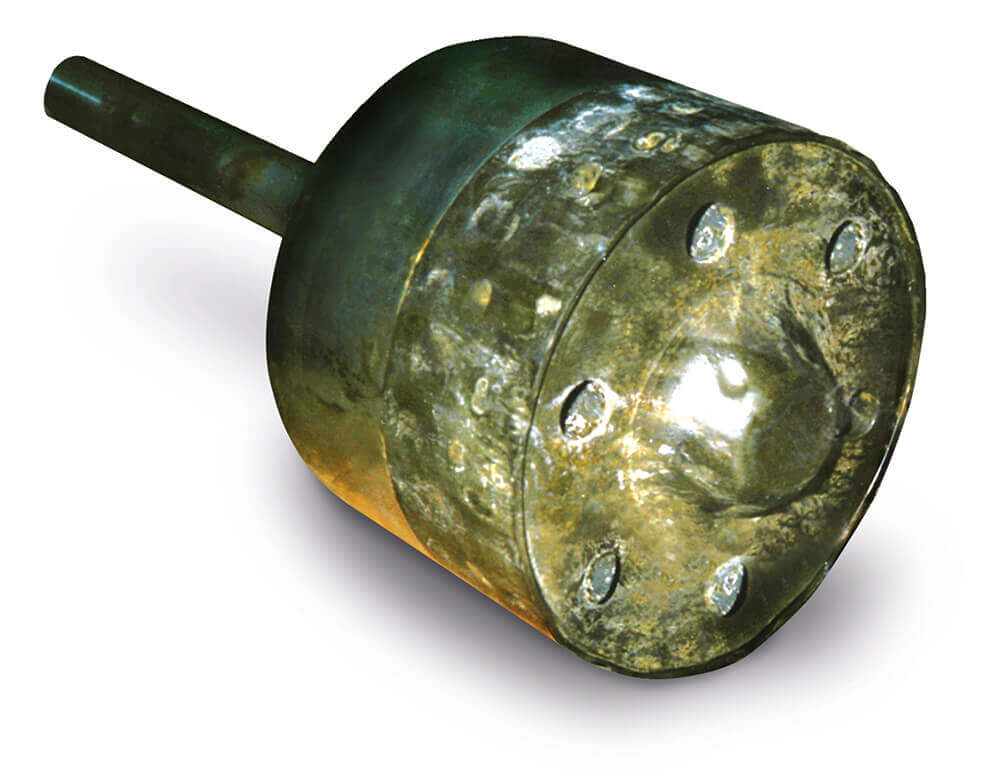
Our many accreditations and processes give you peace of mind when buying from Kent Introl. These include OHSAS 18001, ISO9001, ISO/TS29001, ISO14001, PED Certificate API 6A, API 17D Monogram and more. Visit our Accreditations page to find out more.
We continually invest in all areas of the design, testing and manufacturing process to bring you the right products at the right time, at a competitive price. This gives us ever-greater control over the timing and quality of all aspects of the manufacturing process. Visit our Research and Development page to find out more.
We can assist you right through the lifecycle of your valves and other equipment. Whether you need hands-on servicing and support, or technical training to help your own team, we have the expertise to help you maximise the performance of your valves. Visit our Services page to find out more.