Valve Upgrades & Spares
upgrades and spares
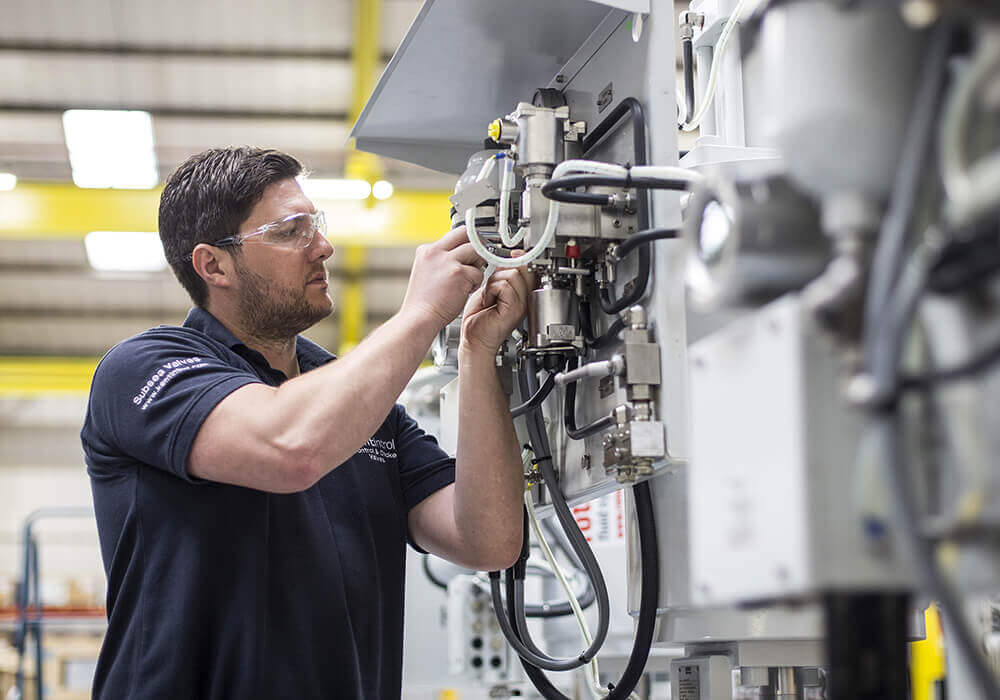
When a valve needs replacing or adapting, we work with you to establish your exact needs. Our engineers will review the process requirements as well as the current and future service conditions.
If the existing valve has failed or hasn’t performed correctly, we will also investigate the issues and their likely causes. For example, we will look at factors such as poor performance, cavitation, flashing, noise, velocity, erosion and pressure drop issues. We will ensure that any such issues are addressed by the final specification.
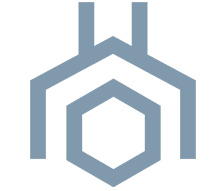
Our focus at all times is on optimising the throughput and life span of valve equipment, by designing and maintaining it to withstand service conditions.
To do this, we follow a specific process for upgrades:
- We issue recommendations for upgrade to materials, trims and other equipment.
- A detailed specification is then created, based on those initial recommendations.
- A 12 months parts guarantee is provided on all upgrade work.
- We provide ongoing specialist support by phone, email or in person on-site as required.
For existing Kent Introl valves, we offer a fast-track replacement service, and we can even advise on upgrades and trim retrofits for third party valve equipment.
In recent years our upgrade and retrofitting service has helped clients all over the world keep their equipment performing even in difficult service conditions. Typical projects include upgrading trims to help avoid sand impurities, changing to carbide and LCV trims to reduce the effects of cavitation and more.
Our many accreditations and processes give you peace of mind when buying from Kent Introl. These include OHSAS 18001, ISO9001, ISO/TS29001, ISO14001, PED Certificate API 6A, API 17D Monogram and more. Visit our Accreditations page to find out more.
We continually invest in all areas of the design, testing and manufacturing process to bring you the right products at the right time, at a competitive price. This gives us ever-greater control over the timing and quality of all aspects of the manufacturing process. Visit our Research and Development page to find out more.
We can assist you right through the lifecycle of your valves and other equipment. Whether you need hands-on servicing and support, or technical training to help your own team, we have the expertise to help you maximise the performance of your valves. Visit our Services page to find out more.