EQUINOR GJØA
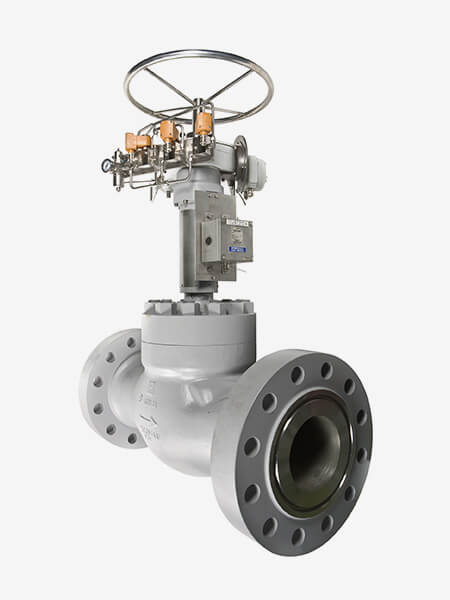
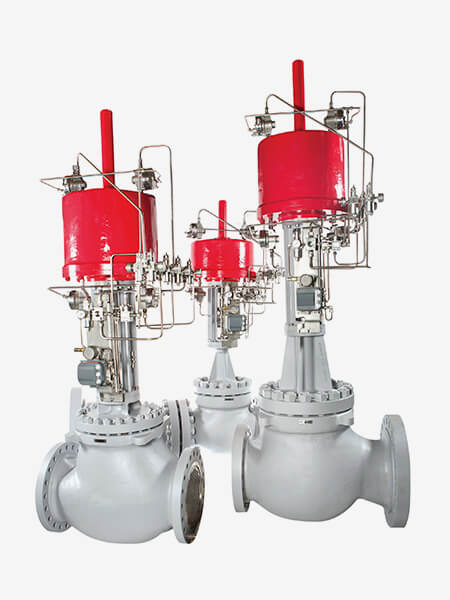
The total delivery to the Gjøa platform exceeded 250 control valves, and 6 surface choke valves, which ranged in size from 1/2” to 24”, with pressure classes ANSI 150 to ANSI 4500. Materials included Titanium, 6Mo, Duplexes, Stainless Steels and Carbon Steels. Solutions included surface choke valves and globe angle valves and rotary control valves. On completion of manufacturing, the valves were shipped to approximately 15 package suppliers across Europe for assembly into fire-water systems, sand cleaning systems, hydrocyclone packages etc, before being delivered finally to the construction yard for installation onto the platform. KKI continued to support the installation and commissioning phases of the project with provision of service engineering resources, as required, at the Aker Stord yard in Norway. During this time, KKI engineers calibrated and tuned the delivered equipment according to the required performance and input.
Ownership of the Gjøa platform has since been transferred from EQUINOR to ENGIE.