SCHEDULED SHUTDOWN
KENT INTROL | UNITED KINGDOM
Project Background
The shutdown took place at one of the UK’s principal oil refineries, with a refining capacity of 296,000 barrels per day. As well as producing around 1/6th of the UK’s petrol requirements, the facility also produces commodities such as jet fuel and diesel. The refinery conducts a rolling programme of maintenance and KKI were called upon to support a shutdown during which over 100 control valves would need to be maintained.
THE REQUIREMENT
The customer originally allocated four weeks for the shutdown, although this subsequently reduced to three. 104 control valves and actuators of sizes ranging from 1” to 12” would be sent to KKI for review and upgrade or maintenance. Since the valves had all originally been produced by Kent Introl (some dating back to the 1970s), the original paperwork was on hand for the KKI team, to support the required work.
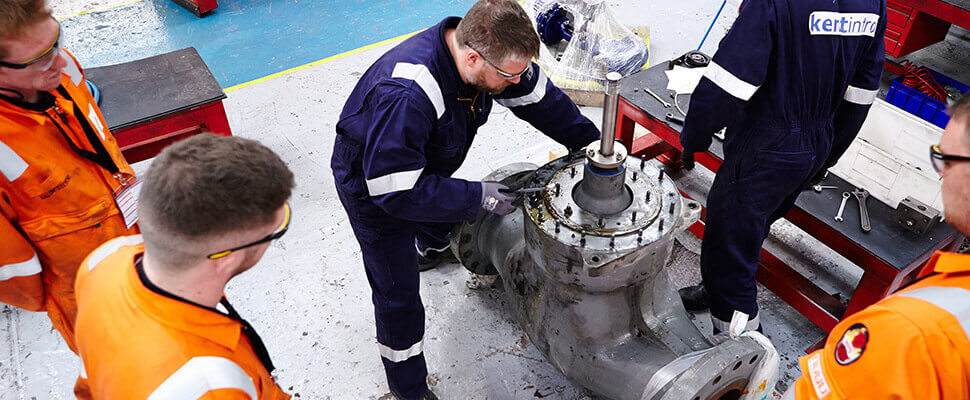
ATTENTION TO DETAIL
A team of 17 was allocated to the project, working 7 days a week to ensure the revised three-week deadline was met. To ensure the project’s smooth and effective running, a system of cataloguing each incoming valve and its component parts was used, ensuring all elements were accounted for at all times. Each valve needed to be stripped, inspected and assessed, cleaned, and its actuator painted before being re-built. It then needed to undergo a body pressure test and seat leakage test and before being re-marked with the customer’s stencilled tag number. A comprehensive paperwork trail accompanied each valve. Understandably, during this process, certain valves were found to be in a worse state of repair than expected. Whilst the overhaul of some valves was completed in a day, others took five working days to complete – including those needing replacement parts such as trims. In these cases, the spare parts were manufactured by KKI at our adjacent production facility, which had been put on stand-by for this work in advance. Where appropriate, reviewed valves were recommended for upgrades such as replacement trim material or changes to actuators. The benefits of our OEM spares, cost and operational efficiency were discussed with the customer’s project team before proceeding.
A FLEXIBLE APPROACH
KKI’s flexible and dynamic approach to the scheduling of work meant that all 104 valves were delivered back to the refinery on time. Only one valve was returned by the customer for further adjustment during the whole project – and even then it was back on-site the following day. The customer’s project managers were extremely complimentary about the quality of the service provided by KKI, declaring themselves ‘more than happy’ during the final project review meeting.
SCHEDULED SHUTDOWN - KENT INTROL