Characterised Choke Valve Trim to Meet Full Production Field Life Conditions
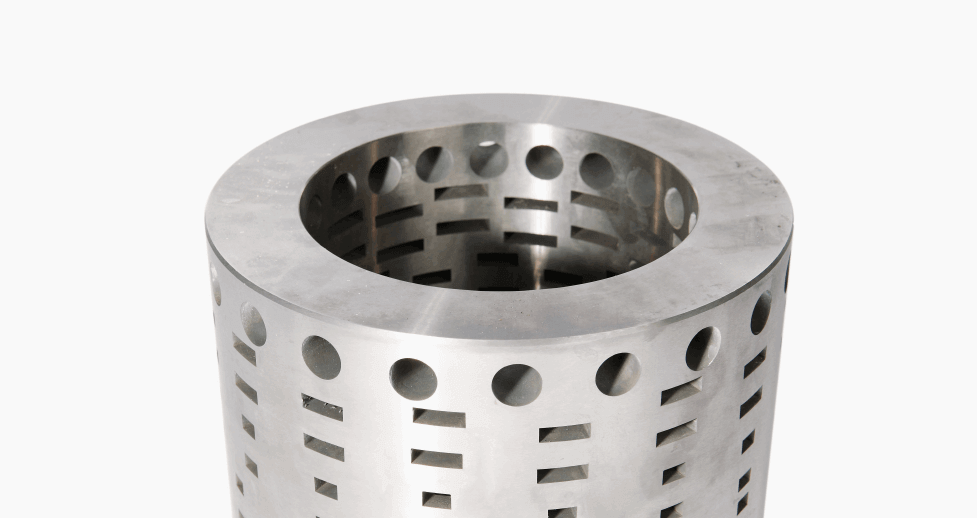
Kent Introl celebrates 30 years of solving control valve challenges with the Vari-stage characterised trim.
We supplied the first Vari-stage trim to Amoco Chemicals Corp in 1987. This 14” ANSI 300 rated control valve with a 12” 50% VHFT (Variable High Friction Triple) stage trim was used in the Polypropylene Plant at Amoco’s Chocolate Bayou facility in Texas. The first 50% of the valve travel had 3 stages of velocity and pressure control and from 50% to fully open it reverted to a single stage.
Over the last 30 years the Vari-stage trim has set the standard in the industry and has been used successfully on hundreds of technically challenging installations across the globe. In 1994 it was used on a specialist surface choke application for the BP Clyde Platform in block 30/17b of the UK North Sea. It was inevitable that the trim design would also be used in one of our own subsea chokes. This happened in 1998 when it was installed on the BP Troika project in the Gulf of Mexico.
More recently the Vari-stage trim has been used to suit the various process parameters that a choke will see throughout its service life. This includes the well start up conditions that initially experience very high pressure drops and high velocities under low choke opening conditions, as well as the end of life conditions when pressures in the well have declined and high capacity flow is required.
This example shows a VectorTM guide that was assembled into one of 20 off chokes that were purchased by a Middle Eastern international oil company. The client’s full life of field predicted production flow scenarios were sent to Kent Introl for a suitable product to be supplied. Kent Introl identified that the initial start-up and early life conditions were very severe, with anticipated pressure drops in excess of 600 bar. Combined with the low flow rates the calculated CV’s at the flowing conditions were quite small. The calculations highlighted that a standard single stage solution was not the answer in this instance as there was high risk of velocity-induced severe erosion.
To accommodate the large pressure drops and subsequent high velocities an 8 stage velocity control section of trim was selected for the first 25% of the choke travel. Over a period of time it was predicted that the pressures in the well would decline and so from 25% to 50% open a 6 stage velocity control section of trim was selected. As the well pressures declined further, a 4 stage velocity control section of trim was selected in the opening percentages between 50% and 75%. Towards the end of field life when the predicted pressures in the wells were expected to be minimal, the client wanted to achieve as much production as possible. At this point Kent Introl proposed a 2 stage section from 75% to 100% opening.
We delivered great value to the client who was able to order choke valves to cover all anticipated flow conditions without the need to replace trims with a larger solution later in the field life. This saved the downtime that would have been required to install new trims as well as the additional costs associated with the purchase of larger trims.
Contact us to find out more about our multi-stage trim valve technology and velocity control valve trims. Our experienced technical team can also work with you to develop choke valves that meet your exact needs. Find out more about our specialist engineered choke valve solutions today.
Subscribe to our newsletter to receive the latest updates from the Kent Introl team. If you enjoyed this article be sure to click the share buttons below!