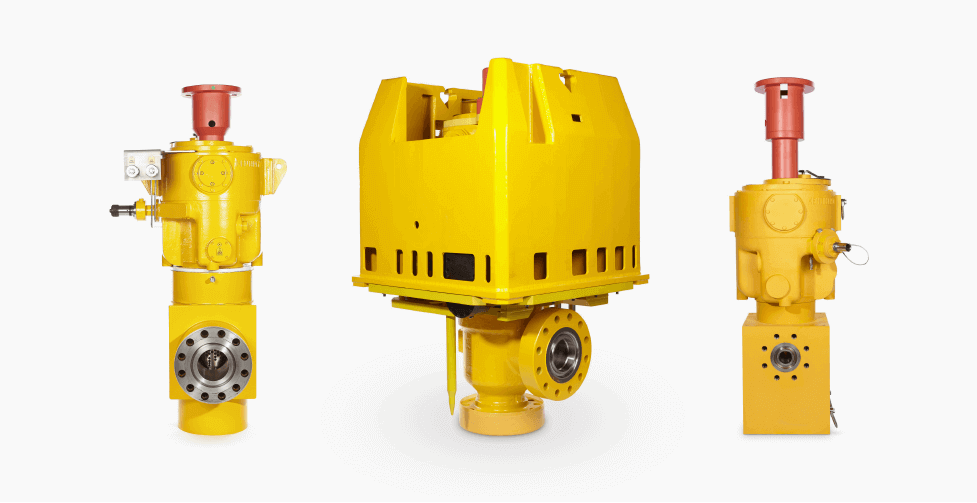
Subsea choke valves are generally installed on Subsea Christmas Trees or in Subsea Flow Manifolds. The subsea choke is the primary pressure and flow regulator on the subsea installation.
Some wells have complex flowing parameters due to the combination of hydrocarbon gases and liquids. In addition to the flow there are added technical challenges of handling very high-pressure drops. These then lead to high velocities and the additional difficulties of entrained solid contaminates in the flow.
Velocity Control Trim Technology
It is common for subsea choke manufacturers to select a single stage pressure reduction trim to handle the most severe flow applications. These solutions incorporate a solid tungsten carbide trim to counter erosion and perform well if the application is not severe service. However high-velocity applications are more susceptible to erosion which can happen quickly if velocity control methodology is not followed.
VectorTM Velocity Control trim technology has been used successfully for a number of years on topside applications. The well fluid is guided through a series of passages at each level on the trim before passing through a three-dimensional flow-path. The area expands after each turn, allowing for the expansion of the gas phases and therefore controlling the velocity.
On liquid applications the Velocity Control principle ensures the choke pressure profile does not drop below the vapour pressure of the medium. This prevents the onset of harmful cavitation. The velocity is also controlled so it does not go beyond the threshold for vibration, erosion and noise.
Non-Collapse Subsea Choke Valve Trim Design
In most subsea choke trim designs the main control/throttling components are manufactured from solid tungsten carbide. Certain grades of tungsten carbide have excellent characteristics to prevent erosion, but tungsten carbide can also be quite brittle. If it is not suitably protected, the subsea choke and tungsten carbide trim could experience a catastrophic failure.
The Kent Introl Brick-Stopper provides three basic functions:
- It is used to hold the whole trim component in cartridge form, assisting subsea insert retrieval.
- As the tungsten carbide is shrunk into the more ductile Brick-Stopper, it is forced into a state of compression. When tungsten carbide is placed in tension the mechanical performance is reduced quite significantly. However when it is in a state of compression, mechanical performance is enhanced.
- The Brick-Stopper prevents direct solid impacts onto the tungsten carbide components which prevents catastrophic failure of the trim.
Over the last 20 years Kent Introl has conducted various choke trim impact tests to ensure that tungsten carbide choke trim components do not experience catastrophic failure when hit by solid contaminates in the flowing medium. The Kent Introl standard Brick-Stopper has been successfully tested up to an impact value of 100 Joules. Kent Introl has also supplied trims that have been tested to 1320 Joules which generally meet the onerous requirements of NORSOK P100.
Our choke valves are designed to meet the needs of the vast majority of applications and in-service conditions. They offer you a wide choice of materials, trim options and sizes. Contact us to find out how the Kent Introl subsea solutions, including subsea choke valves, can help to maximise the performance and minimise the downtime of severe service applications.
Subscribe to our newsletter to receive the latest updates from the Kent Introl team. If you enjoyed this article be sure to click the share buttons below!